Useful Tech Tips from Trailer Sales & Service, Inc. in Newton, North Carolina
Here are some helpful tech tips to help with situations the customers at Trailer Sales & Service, Inc. tend to come across. Many of these involve roll-up door repairs and air suspension maintenance. As always, call us to schedule an appointment at 828-465-1800 to have one of our techs assist or bring it by!
Cable Replacement
Cable Replacement on Two-Spring Type Balancer
One of the most important procedures to remember about a two spring operator is that it is worked on with the door open. In order to change cables on this style balancer assembly proceed as follows:
- Open door.
- Push door back into horizontal track so that bottom panel is approx. 16" from header. Two men will be needed for this.
- Securely place a clamp in each track, just below the bottom roller. As a point of safety, make certain that clamps are tight on tracks.
- Determine what type of installation you have, either a standard or a shallow header. In a standard header the balancer is clearly visible. The header will measure at least 6", whereas in a shallow header the balancer is somewhat concealed, rather difficult to work on and header measures approx. 5".
- Using a 7/16 " box wrench, loosen two set screws in winding cone.
- Make sure spring assembly is free and can spin easily on shaft.
- Wind new cable onto cable drum. Make certain that the cable follows the grooves as it is possible to install them backwards! In a regular installation, cable comes off the bottom of drum. In shallow header, cable comes off the top of drum.
- Begin winding balancer by inserting bar into winding cone and pulling down for standard installation, or by pushing up in a shallow header.
- Start counting turns as soon as the cone rotates. 3 1/2 to 4 turns would be correct.
- After the correct turns have been applied, tighten both set screws securely.
- Carefully remove both clamps in the tracks.
- Lower door and test. A properly balanced door should not fly open, nor fall closed.
Caution! Work on doors and related parts can, in some cases, be dangerous. Any person not experienced and trained in roll up truck door repairs and installation, should consider leaving the work to those who are. Serious injury could result.
Information provided by Whiting Door Manufacturing Corp.
Bottom Panel Replacement
How to Replace a Bottom Door Panel
- Close door until bottom panel is approx. one inch from bottom sill
- Using "C" clamps, securely clamp cables to the posts.
- Remove cables from bottom panel.
- Place two clamps in track above panel to be changed. These clamps will prevent the upper panels from dropping when bottom panel is taken out. To do this, clamps are positioned below the roller.
- Remove roller covers of bottom panel, four places.
- Remove rollers.
- Drill out all rivets on panel.
- Remove panel.
- Insert new panel.
- Install bottom rollers, two places.
- Connect cables to new panel.
- Remove upper clamps installed in step 4.
- Remove clamps on cables.
- Drill new panel for fasteners.
- Raise door slightly and insert new fasteners.
- Tighten fasteners.
- Install rollers and spacer washers at first joint.
Caution! Work on doors and related parts can, in some cases, be dangerous. Any person not experienced and trained in roll up truck door repairs and installation, should consider leaving the work to those who are. Serious injury could result.
Information provided by Whiting Door Manufacturing Corp.
Intermediate Panel Replacement
Replacement of Intermediate Door Panel
- Close door and lock.
- Place two clamps in track above panel to be changed. These clamps will prevent the upper panels from dropping when panel is taken out. To do this, clamps are positioned below the roller.
- Remove roller covers of panel to be changed.
- Remove rollers.
- Drill out all rivets on panel.
- Lift up on door slightly and remove panel.
- Insert new panel.
- Drill new panel for fasteners.
- Lift up on door slightly, again, and tilt back new panel.
- Insert new fasteners.
- Reinstall new panel.
- Tighten fasteners, open door.
Caution! Work on doors and related parts can, in some cases, be dangerous. Any person not experienced and trained in roll up truck door repairs and installation, should consider leaving the work to those who are. Serious injury could result.
Information provided by Whiting Door Manufacturing Corp.
Door Operator Replacement
One of the most important procedures to remember about a two spring Whiting balancer is that it is worked on with the door open. In order to remove this style balancer assembly proceed as follows:
- Open door.
- Push door back into horizontal track so that bottom panel is approx. 16" from header. Two men will be needed for this.
- Securely place a clamp in each track, just below the bottom roller. As a point of safety, make certain that clamps are tight on tracks.
- Determine what type of installation you have, either a standard or a shallow header. In a standard header the balancer is clearly visible. The header will measure at least 6", whereas in a shallow header the balancer is somewhat concealed, rather difficult to work on and header measures approx. 5".
- Place a 3/8" x 12" bar into one of the winding cones located near center of balancer shaft.
- Using a 1/2" wrench, remove both nuts which hold the clamp onto the center balancer bracket.
- While holding spring tension on bar with one hand, remove clamp. Note, with a standard header, spring tension will be in the direction to cause bar to go up. With a shallow header, tension will cause bar to go down.
- With another bar, walk tension off of springs by either using alternate winding cones, or the same cone. Another method would be to use just one bar and on open end wrench on squared portion of balancer shaft.
- Once all tension has been removed, unhook both cables from cable drums and remove cotter pin nearest to end of balancer shaft.
- Shift balancer to the side and withdraw from bracket. If sufficient travel is not possible, loosen set screws from spring assembly, slide spring towards center and then withdraw.
In order to replace this style balancer, proceed as follows:
- Remove both cables from door and install onto cable drums. Make certain that the cable follows the grooves as it is possible to install them backwards! Wind cable onto drum leaving approx. 12" of cable out. Secure cable by winding 4 or 5 layers of masking tape on cable as it leaves drum.
- Install a cotter pin in balancer shaft hole farthest from end. Remember to set the cotter pin properly. If not, it could interfere with drum rotation.
- Install shaft into brackets. In standard header, red end goes on roadside. In shallow header, red end goes to the curbside.
- Install and set cotter pin closest to end of shaft.
- Connect cables to door.
- Begin winding balancer by inserting bar into winding cone and pulling down for standard installation, or by pushing up in a shallow header.
- Start counting turns as soon as the cone rotates. 3 1/2 to 4 turns would be correct.
- After the correct turns have been applied, insert center clamp over the bracket and tighten both nuts securely.
- Carefully remove both clamps in the tracks.
- Lower door and test it. A properly balanced door should not fly open, nor fall closed.
Caution! Work on doors and related parts can, in some cases, be dangerous. Any person not experienced and trained in roll up truck door repairs and installation, should consider leaving the work to those who are. Serious injury could result.
Information provided by Whiting Door Manufacturing Corp.
Preventative Maintenance for Air Bags
Air Spring Suspension Preventative Maintenance Checklist
Listed below are items that can be checked when the vehicle is in for periodic maintenance.
NOTE: Never attempt to service the air suspension on a truck or trailer with the air springs inflated.
Inspecting Air Springs
- Inspect the O.D. of the air spring. Check for signs of irregular wear or heat cracking.
- Inspect air lines to make sure contact doesn't exist between the air line and the O.D. of the air spring. Air lines can rub a hole in an air spring very quickly.
- Check to see that there is sufficient clearance around the complete circumference of the air spring while at its maximum diameter.
- Inspect the O.D. of the piston for buildup of foreign materials. (On a reversible sleeve style air spring, the piston is the bottom component of the air spring).
- Correct ride height should be maintained. All vehicles with air springs have a specified ride height established by the O.E.M. manufacturer. This height, which is found in your service manual, should be maintained within 1/4". This dimension can be checked with the vehicle loaded or empty.
- Leveling valves (or height control valves) play a large part in ensuring that the total air spring system works as required. Clean, inspect and replace, if necessary.
- Make sure you have the proper shock absorbers and check for leaking hydraulic oil and worn or broken end connectors. If a broken shock is found, replace it immediately. The shock absorber will normally limit the rebound of an air spring and keep it from overextending.
- Check the tightness of all mounting hardware (nuts and bolts). If loose, re-torque to the manufacturer's specifications. Do not over-tighten.
Cleaning Air Springs
Approved cleaning media are soap and water, methyl alcohol, ethyl alcohol and isopropyl alcohol.
Non-approved cleaning media include all organic solvents, open flames, abrasives and direct pressurized steam cleaning.
The total inspection process should be included as part your comprehensive Preventative Maintenance Program.
This information provided by Firestone
Air Spring Identification
Shock Absorber Maintenance
Replace Shock as part of your established Preventative Maintenance Program
Tires are expensive!.......No duh, right?
Well a very important, but lesser known Preventative Maintenance procedure is the replacement of shock absorbers on a preventative, rather than a corrective maintenance basis. Shock absorbers have become one of the major causes of unnecessary tire wear, as well as the cause of jarring and vibration damage to many other components. The reason for this phenomenal increase in worn shock related damage is the advent of soft air suspensions on trailers coupled with the deteriorating condition of the nation's roadways have made shock replacement an important step in extending tire life. The ATA's TMC Recommended Practice on air suspension maintenance (RP 643) recommends that fleets "Establish a preventative maintenance procedure which changes shocks on a regular basis". This needs to be performed BEFORE a problem arises. Which had you rather replace? Shocks are cheaper to replace than tires.
When a new tire is installed on a trailer, the shock absorber may look fine, but if it has been run over 150,000 miles, it will have stroked over 30 million times. Since the shock's hydraulic fluid does not have the lubrication quality of engine oil, it will have lost much of its dampening capabilities due to internal wear. When a shock loses over 50% of its dampening, it can allow the excessive wheel hop on rough roads that can cause irregular tire wear due to excessive foot print distortion.
Bottom Line – Set an maintain a set schedule for replacing your shock absorbers as part of a quality.
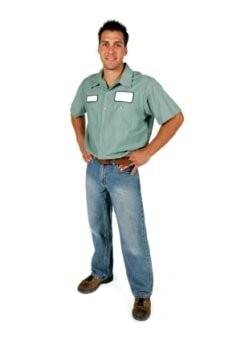